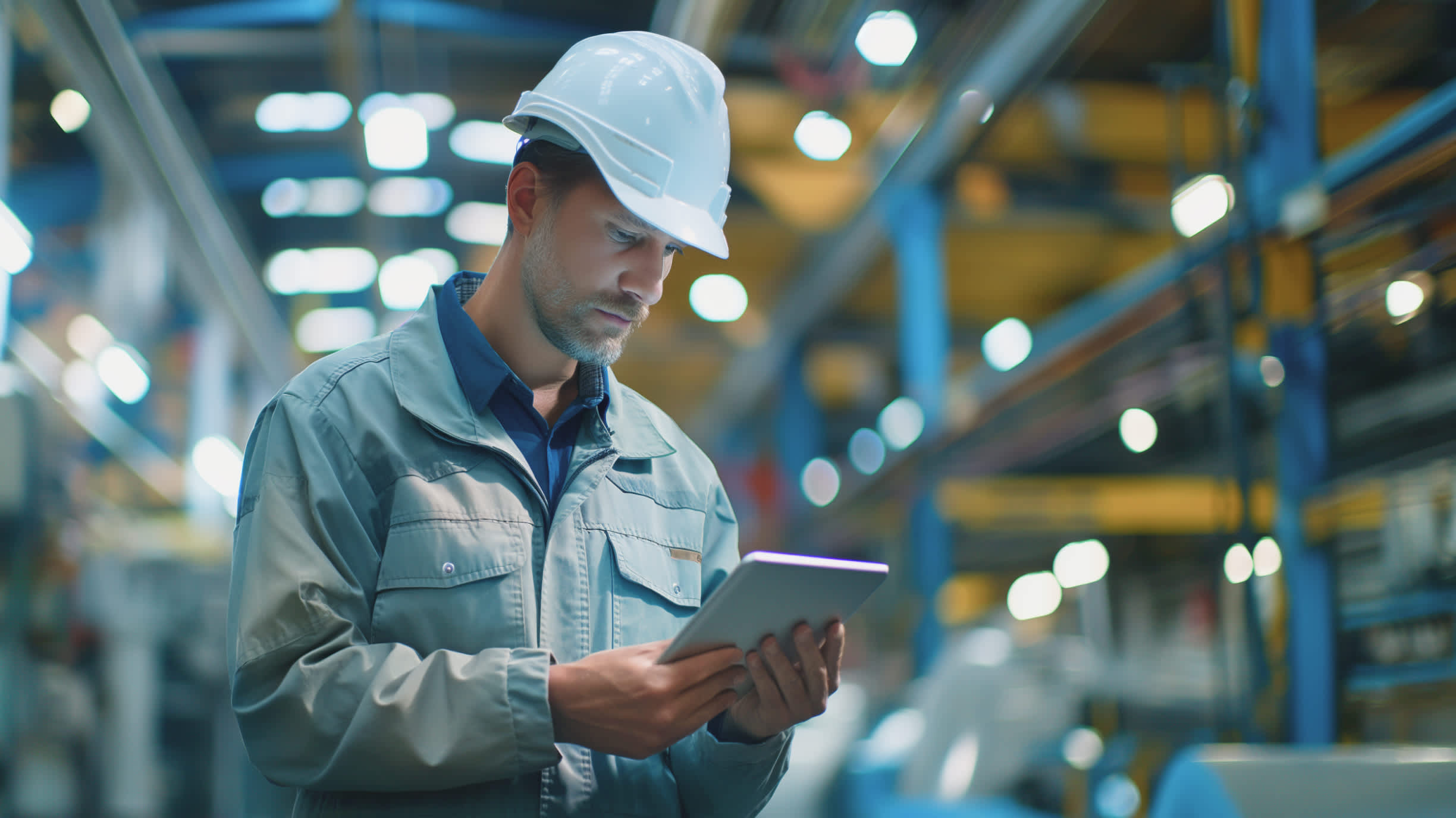
In the ever-evolving world of light industry, characterized by the production of consumer goods and less capital-intensive products compared to heavy industry like steel or automobile manufacturing, technological advancements are driving a transformative wave. Sectors such as logistics, distribution, manufacturing, warehousing, and consumer goods are experiencing technological transformations that are significantly boosting efficiencies. Technological advancements will redefine temporary staffing practices within the light industry.Â
These industries are undergoing a profound shift from the integration of cutting-edge robotics to the use of insightful data analytics. Technology is addressing key challenges in the light industry by using data to mitigate market demand volatility, enhancing safety to comply with changing regulations, streamlining supply chain complexity through advanced analytics, and leveraging technology platforms to find temporary talent for peak seasons.
But why does this matter? It's simple: in an increasingly competitive global market, staying ahead of the curve is key. Companies that fail to adapt risk being left behind. Moreover, for workers, technological advancements represent more than just a change in tools; they are catalysts for upskilling, greater visibility into opportunities, better safety measures, and improved working conditions.
So, let's dive deeper into technology's role in reshaping the landscape of light industry across the United States. By understanding the nuances of this shift, we can appreciate how innovation isn't just driving success—it's shaping the future of work for generations to come.
Leveraging digital tools to thriveÂ
In today's dynamic economic landscape, companies in light industry must swiftly respond to shifts that impact demand and supply. By leveraging real-time data, businesses gain the agility to optimize operations and adjust to fluctuating demands effectively. However, amid this adaptation, a paramount need arises for companies to prioritize the reliability and quality of their workforce. At Job&Talent, we address these challenges through our innovative staffing solution. Our digital shift planning and management features incorporate real-time attendance data, enabling managers to make immediate adjustments. Additionally, we use attendance statistics to identify trends and mitigate productivity downtimes, ensuring a more consistent workflow.
To further enhance efficiency, our smart clocking features with geolocation-based reminders help workers clock in promptly, reducing tardiness and absenteeism. By leveraging these technologies, companies can access real-time data for informed decision-making, while workers receive incentives to bolster their reliability. Balancing these facets ensures not only a smoother operational journey for companies but also a more enriching experience for both employers and workers, fostering a symbiotic relationship built on trust and efficiency.
Enhanced safety measures
Safety is paramount in any industrial environment, and technology is bolstering safety measures in remarkable ways. From sensor-equipped machinery that detects potential hazards to wearable devices that monitor workers' health and movements, technology is creating safer workplaces and reducing the risk of accidents. By harnessing the power of data analytics, Job&Talent helps companies proactively identify safety trends so they can implement targeted interventions. In other words, technology is creating a paradigm shift towards proactive risk management, ensuring that workers return home safely at the end of each day. In order to fully leverage this data for insights, companies need to ensure they are capturing this data and should ensure partners they work with are also data-driven.Â
Optimized supply chain management
In the fast-paced light industrial industry, efficient supply chain management is key to success. With the advent of sophisticated software solutions and data analytics tools, companies can optimize inventory management, track shipments in real time, and predict demand with greater accuracy, leading to smoother operations and satisfied customers. From the perspective of temporary work, efficient supply chain management is vital. Temporary workers often support peak periods or special projects, and optimized supply chain processes ensure their seamless integration, maximizing productivity and contribution to overall success. Support for fluctuating demands for temporary workers should also be optimized. Temporary staffing agencies should focus on the ability to adapt to demands while ensuring the quality of workers does not deteriorate for quick turnarounds.Â
Empowering workers with training and development
Technology isn't just about machines; more than anything, it’s about empowering people. With the rise of online learning platforms and interactive training modules, workers in light industry have access to unprecedented opportunities for skills development and career advancement. By investing in the growth and development of their workforce, companies can foster a culture of continuous improvement and innovation. Moreover, with the ongoing talent shortage, technology-driven upskilling can help fill the workforce gaps that companies are struggling to fill.Â
Especially for companies employing temporary workers, technology-enabled training initiatives are particularly valuable. Temporary workers often play a crucial role in supporting peak periods or special projects within the light industry. By providing access to online learning platforms, companies can ensure that temporary workers have the skills and knowledge necessary to hit the ground running from day one. This not only maximizes their productivity but also enhances their job satisfaction and performance.
Streamlined operations with automation
Automation is no longer a buzzword; it's a game-changer in light industrial settings. Advanced robotics and automated systems streamline processes, increase effectiveness, and reduce human error across manufacturing, logistics, and warehousing. In manufacturing, robotic arms and automated machinery accelerate production cycles with high accuracy. In logistics, automated guided vehicles and conveyor systems optimize material handling, reducing manual labor. Warehousing benefits from automated inventory management systems that use barcode scanning and RFID technology for real-time tracking and efficient order fulfillment.
Despite these advancements, the human element remains essential. Recruiters, shift managers, and on-site managers make critical decisions, solve complex problems, and ensure worker effectiveness. Their ability to innovate and adapt complements automation, driving progress in light industry. While automation enhances efficiency, the human touch brings creativity and adaptability, ensuring continued success in the digital age.
At Job&Talent, we're proud to be at the intersection of technology and talent, driving positive change in the light industry across the US. Ready to take your light industrial operations to the next level? Get in touch with us today to learn how our innovative staffing solutions can help you thrive in the digital age. Book a demo here.